Easy methods to mill small steel portions unlocks a global of precision production. From intricate gears to minuscule parts, this information dives deep into the tactics, fabrics, and design concerns a very powerful for good fortune.
This complete breakdown covers the whole lot from choosing the right milling device and fabrics to optimizing tooling and reducing parameters, making sure height efficiency and high quality for your tasks.
Advent to Steel Milling: How To Mill Small Steel Portions
Steel milling is a a very powerful machining procedure for growing intricate and exact small steel portions. It comes to the usage of a rotating reducing device, generally a milling cutter, to take away subject material from a workpiece. This subtractive production method lets in for the manufacturing of advanced geometries, making it crucial in more than a few industries, from aerospace to shopper electronics. The method is especially well-suited for growing small portions with exact tolerances and complicated shapes which are tough or inconceivable to succeed in with different strategies.Milling machines, particularly the ones designed for smaller portions, regularly function complex options like programmable controls and high-precision measuring equipment to make sure correct manufacturing.
Those machines are moderately engineered to deal with the particular forces and subject material elimination traits required for growing those parts.
Sorts of Milling Machines for Small Portions
More than a few milling device varieties cater to other wishes and scales of manufacturing. The selection is determined by the scale and complexity of the portions being milled. Variety is regularly pushed by way of elements equivalent to required precision, subject material sort, and manufacturing quantity.
- Vertical Milling Machines: Those machines are steadily used for milling small portions because of their talent to house quite a few reducing equipment and their moderately compact footprint. They supply just right balance and keep watch over over the reducing procedure, crucial for precision paintings on smaller parts. Their vertical spindle orientation facilitates the milling of intricate options in numerous planes.
- Horizontal Milling Machines: Those machines excel in large-scale manufacturing, or when high-volume manufacturing of moderately easy shapes is wanted. Horizontal milling machines be offering a bigger paintings space in comparison to vertical machines, however their use for small portions is much less commonplace because of the bigger measurement and setup time. They’re typically most popular for greater portions or portions requiring intensive floor machining.
- CNC Milling Machines: Laptop Numerical Regulate (CNC) milling machines are broadly used for small portions production because of their talent to accomplish advanced cuts with excessive precision and repeatability. CNC machines are managed by way of pc methods, bearing in mind exact motion of the milling cutter to succeed in advanced shapes. This programmable keep watch over is valuable in growing custom designed or extremely detailed portions.
Elementary Rules of Milling
Working out the elemental ideas of milling is significant for environment friendly and exact machining. The reducing forces and subject material elimination are a very powerful facets to believe.
- Chopping Forces: Forces generated throughout the milling procedure are influenced by way of elements like the fabric hardness, reducing pace, and feed charge. Prime reducing forces may end up in device vibration or device breakage if no longer controlled correctly. Right kind number of reducing parameters, like reducing pace, feed charge, and intensity of reduce, minimizes those forces. Working out and controlling those forces is a very powerful for keeping up the standard of the completed phase.
- Subject matter Elimination: The milling procedure necessarily comes to eliminating subject material from the workpiece. The fabric elimination charge (MRR) is determined by the reducing device’s geometry, the reducing pace, the feed charge, and the intensity of reduce. The MRR is the most important consider figuring out the full potency of the machining procedure. Environment friendly subject material elimination guarantees that the method is optimized for pace and high quality.
Comparability of Milling System Varieties
System Kind | Suitability for Small Portions | Benefits | Disadvantages |
---|---|---|---|
Vertical Milling Machines | Prime | Compact, exact, just right keep watch over | Restricted paintings space |
Horizontal Milling Machines | Low | Massive paintings space, excessive quantity doable | Much less exact for small portions |
CNC Milling Machines | Very Prime | Prime precision, advanced shapes, programmable | Upper preliminary charge, calls for setup |
Subject matter Variety and Concerns
Selecting the proper subject material is a very powerful for a success milling of small steel portions. The fabric’s houses immediately have an effect on the machining procedure, device lifestyles, phase high quality, and general cost-effectiveness. Elements like energy, hardness, and machinability should be moderately evaluated to make sure the general product meets design specs and manufacturing objectives. A deficient subject material variety may end up in pricey transform, delays, and in the long run, product failure.Deciding on the right kind subject material for a small steel phase isn’t simply a question of choosing the most affordable choice.
It calls for a complete figuring out of the phase’s supposed serve as, the working setting, and the milling procedure itself. This figuring out guides the choice procedure, making sure that the selected subject material possesses the important traits for environment friendly and top of the range machining.
Elements Affecting Subject matter Variety
Subject matter houses are paramount in figuring out the suitability of a subject material for milling. Those houses affect the convenience and potency of the machining procedure, and immediately have an effect on the general phase’s high quality.
- Energy: The power of a subject material to resist pressure with out failure is a very powerful. Prime energy fabrics are important for portions that should undergo important so much. A powerful subject material can withstand deformation throughout the milling procedure, which prevents undesirable warping or distortion of the general phase.
- Hardness: Hardness refers to a subject material’s resistance to indentation or scratching. Onerous fabrics regularly require specialised reducing equipment and strategies, impacting the milling procedure’s potency and doubtlessly expanding prices. The hardness of the fabric must be balanced in opposition to the specified precision and end of the phase.
- Machinability: That is the convenience with which a subject material may also be machined. Machinability elements come with chip formation, device put on, and reducing forces. Fabrics with just right machinability are processed extra successfully and scale back device put on, resulting in decrease prices and better manufacturing charges.
Not unusual Fabrics for Small Steel Portions
More than a few fabrics are hired for small steel portions, each and every with its distinctive houses. The selection is determined by the particular utility and required traits.
Subject matter | Homes | Suitability for Milling |
---|---|---|
Aluminum Alloys | Light-weight, just right machinability, moderately low energy | Superb for portions requiring excessive manufacturing charges and lightweight weight. Appropriate for programs the place energy isn’t a number one fear. |
Metal Alloys (e.g., Stainless Metal) | Prime energy, just right put on resistance, regularly corrosion-resistant | Appropriate for portions requiring excessive energy, however is also tougher to device because of upper hardness. Calls for extra powerful reducing equipment and strategies. |
Brass | Just right machinability, moderately low charge, just right corrosion resistance | Appropriate for programs requiring average energy and corrosion resistance, with moderately simple machining. |
Titanium Alloys | Prime strength-to-weight ratio, very good corrosion resistance, excessive hardness | Difficult to device because of excessive hardness and energy. Calls for specialised equipment and strategies for environment friendly machining. |
Demanding situations in Milling Other Fabrics
Other fabrics provide distinctive demanding situations throughout the milling procedure. Working out those demanding situations lets in for higher making plans and optimized machining methods.
- Prime-strength fabrics like hardened steels or titanium alloys may end up in fast device put on, requiring common device adjustments and doubtlessly upper machining prices.
- Brittle fabrics would possibly shatter or crack throughout the milling procedure, necessitating cautious keep watch over of reducing parameters to forestall harm.
- Fabrics with deficient machinability would possibly generate over the top warmth, resulting in device deformation or phase distortion. Environment friendly cooling methods are regularly important.
Tooling and Chopping Parameters
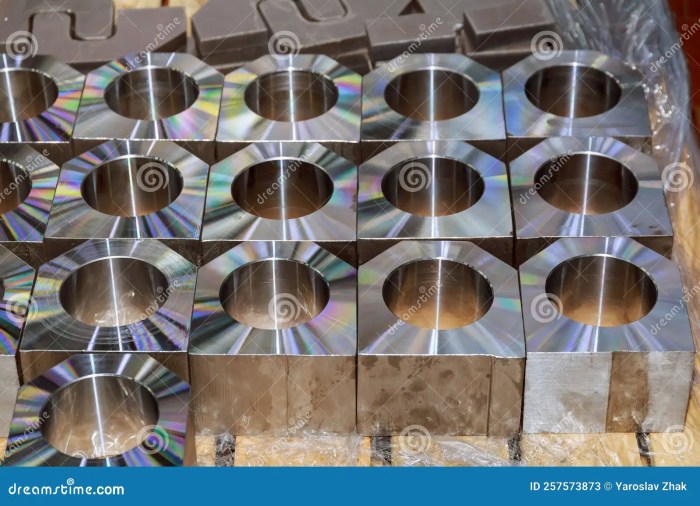
Selecting the proper equipment and surroundings the right kind reducing parameters are a very powerful for attaining top of the range machining of small steel portions. Incorrect variety may end up in deficient floor end, over the top device put on, or even phase harm. Cautious attention of those elements guarantees potency and precision within the milling procedure.
Milling Cutter Variety for Small Portions
Deciding on the correct milling cutter is paramount for a success machining of small portions. Elements equivalent to cutter diameter, selection of tooth, and subject material composition are essential concerns. For intricate geometries or small options, smaller diameter cutters are preferable to reduce the have an effect on of device overhang and deal with exact keep watch over. Multi-flute cutters, with their higher reducing edges, can fortify subject material elimination charges and scale back device put on.
The fabric of the cutter must fit the fabric of the workpiece for optimum efficiency. Prime-speed metallic (HSS) cutters are regularly appropriate for plenty of commonplace fabrics, whilst carbide cutters are most popular for more difficult or extra abrasive fabrics.
Significance of Chopping Parameters
Right kind reducing parameters, together with feed charge, reducing pace, and intensity of reduce, considerably have an effect on the machining procedure. An optimum steadiness is very important to succeed in the specified result. Too excessive a feed charge may end up in chatter and deficient floor end, whilst too low a charge would possibly lead to over the top machining time. Chopping pace influences the device’s lifestyles and the standard of the completed phase.
Intensity of reduce impacts subject material elimination charge and gear loading. Optimizing those parameters reduces cycle time, improves device lifestyles, and yields a top of the range product.
Chopping Parameters Desk
Cutter Kind | Subject matter | Chopping Pace (m/min) | Feed Price (mm/teeth) | Intensity of Reduce (mm) |
---|---|---|---|---|
Prime-Pace Metal (HSS) | Gentle Metal | 100-250 | 0.1-0.3 | 1-2 |
Carbide | Aluminum Alloy | 200-400 | 0.15-0.5 | 1-3 |
Carbide | Stainless Metal | 100-200 | 0.05-0.2 | 0.5-1.5 |
Notice
Those are common tips. Particular values must be made up our minds by way of experimentation and attention of subject material houses, cutter geometry, and desired end.*
Affect of Software Geometry on Machining Efficiency
Software geometry, encompassing the form and attitude of the cutter, performs a vital position within the machining procedure. The rake attitude, clearance attitude, and nostril radius immediately affect chip formation, reducing power, and gear lifestyles. A correctly designed device geometry minimizes friction, promotes environment friendly chip elimination, and ends up in higher floor end. A deficient geometry, alternatively, may end up in over the top device put on, vibrations, and lowered machining potency.
Right kind device geometry variety is a very powerful for optimizing the milling procedure and acquiring the specified high quality and precision within the ultimate product.
Milling Processes for Small Portions
Precision machining of small steel portions calls for specialised milling methods. The intricate geometries and tight tolerances regularly require cautious attention of the milling procedure to make sure optimum effects. Selecting the proper procedure considerably affects the potency, accuracy, and cost-effectiveness of all of the production operation.More than a few milling tactics, starting from simple face milling to intricate slot milling, be offering distinct benefits and drawbacks in small phase manufacturing.
Working out those variations is a very powerful for settling on essentially the most appropriate method for a specific part.
Face Milling Methods
Face milling is a foundational milling operation, supreme for machining flat surfaces. In small phase manufacturing, it is regularly used for growing wide, uniform faces, getting ready surfaces for next operations, or eliminating important subject material. For instance, a big flat phase on a housing part might be successfully milled the usage of a face milling cutter. The precision of the consequent floor is determined by the standard of the cutter, feed charge, and intensity of reduce.
Slot Milling for Actual Grooves
Slot milling is essential for growing intricate grooves and slots. Its utility in small portions production is intensive, enabling the introduction of options like keyways, mounting slots, or air flow channels. The intensity and width of the slot are a very powerful concerns, influencing the accuracy and the fabric elimination charge. The number of the correct milling cutter and reducing parameters are essential for attaining exact dimensions and fighting device breakage.
Finish Milling for Advanced Shapes
Finish milling is a flexible operation in a position to generating advanced shapes, contours, and lines on small portions. Its flexibility stems from the supply of more than a few finish mill geometries and sizes. Finish turbines can successfully deal with intricate shapes, growing recesses, wallet, or grooves. Imagine a equipment part; finish milling can create the equipment tooth with excessive precision.
The collection of finish mill is determined by the specified geometry, the fabric being milled, and the specified floor end.
Comparability of Milling Processes
Milling Procedure | Strengths | Weaknesses |
---|---|---|
Face Milling | Prime subject material elimination charge, appropriate for enormous flat surfaces, moderately easy setup. | Restricted capacity for advanced shapes, would possibly require a couple of passes for intricate portions. |
Slot Milling | Creates exact grooves and slots, appropriate for intricate options. | Decrease subject material elimination charge in comparison to face milling, doable for device breakage if no longer moderately managed. |
Finish Milling | Flexible, in a position to machining advanced shapes, excessive precision achievable. | Will also be difficult to arrange for intricate portions, doubtlessly slower than face milling for enormous flat surfaces. |
Instance: Milling a Equipment
A equipment’s intricate tooth require precision finish milling. A high-speed metallic finish mill with a particular geometry is chosen to compare the equipment’s teeth profile. The milling procedure comes to a couple of passes, making sure exact teeth shapes and correct spacing. Right kind number of reducing parameters, like feed charge and intensity of reduce, is significant for optimum efficiency and minimum device put on.
The completed equipment will show off excessive accuracy and reliability, a very powerful for its serve as in a mechanical machine.
Design Concerns for Milling Small Portions
The design of small steel portions performs a a very powerful position in figuring out the potency and cost-effectiveness of the milling procedure. Cautious attention of phase geometry, subject material houses, and tooling alternatives can considerably have an effect on the full machining time, device lifestyles, and ultimate phase high quality. Optimizing the design for milling reduces waste and improves the precision of the completed product.Right kind phase design interprets immediately into environment friendly milling operations.
By means of expecting doable demanding situations throughout the machining procedure, designers can proactively incorporate answers that reduce machining time and maximize using the device. Working out how other geometries have an effect on reducing forces and gear lifestyles is essential to growing designs which are each sensible and economical.
Affect of Phase Geometry on Chopping Forces and Software Lifestyles
Phase geometry immediately influences the reducing forces encountered throughout the milling procedure. Advanced shapes, sharp corners, and deep wallet require extra power, doubtlessly main to better put on at the reducing device and lowered device lifestyles. Conversely, easy shapes with clean transitions and well-defined options usually lead to decrease reducing forces and longer device lifestyles. This idea applies throughout more than a few fabrics and milling processes.
Working out the connection between geometry and reducing forces lets in for knowledgeable design alternatives to reduce put on and lengthen device lifestyles. The collection of reducing device and feed charges may also be adjusted in response to those elements.
Design Rules for Minimizing Machining Time and Maximizing Potency
A number of design ideas can considerably reduce machining time and maximize potency throughout the milling of small portions. Symmetry partly design, for instance, lets in for extra balanced subject material elimination and decreases the full machining time. The usage of clean transitions between options reduces the possibility of device breakage and improves floor end. Good enough subject material give a boost to and reinforcement inside the design are essential to fighting phase deformation throughout the machining procedure.
Desk of Design Concerns for More than a few Small Phase Geometries
Phase Geometry | Design Attention | Affect on Milling |
---|---|---|
Easy Shapes (e.g., rectangles, squares) | Instantly edges and uniform thickness | Low reducing forces, longer device lifestyles, quicker machining. |
Advanced Shapes (e.g., with wallet, grooves, and undercuts) | Optimized device paths, subject material give a boost to, and clearance | Upper reducing forces, doable for device breakage if no longer optimized, higher machining time. |
Portions with Undercuts | Right kind design to permit device get right of entry to with out inflicting phase deformation | Cautious making plans of device paths is significant to forestall deformation or breakage. |
Portions with Sharp Corners | Rounded corners or chamfers to cut back pressure focus | Sharp corners can build up reducing forces and gear put on, doubtlessly resulting in untimely device failure. |
Portions with Holes | Enough clearance round holes for device get right of entry to and chip evacuation | Incorrect clearance may end up in chip accumulation, device interference, and lowered potency. |
High quality Regulate and Inspection
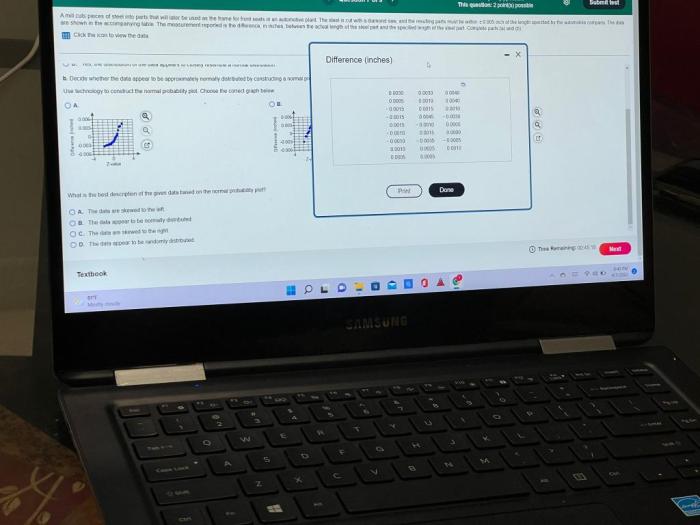
Making sure precision and high quality in milled small portions is paramount. A powerful high quality keep watch over procedure safeguards in opposition to defects, making sure the general product meets the supposed specs and buyer necessities. That is essential for keeping up an organization’s popularity and keeping off pricey transform or product recollects.Correct inspection strategies are crucial to hit upon deviations from the specified dimensions and floor finishes.
This proactive method minimizes the chance of faulty portions achieving the buyer, fighting doable disasters and keeping up the reliability of the general product.
Significance of High quality Regulate in Milling Small Portions, Easy methods to mill small steel portions
High quality keep watch over in milling small portions is a very powerful for a number of causes. At the beginning, it promises dimensional accuracy, making sure the portions are compatible exactly into their supposed assemblies. Secondly, it maintains constant floor finishes, impacting the phase’s aesthetic enchantment and resistance to put on and corrosion. Thirdly, it minimizes the manufacturing of faulty portions, saving time and assets, and making sure buyer pride.
In the end, it facilitates steady development within the milling procedure, bearing in mind changes and optimizations to deal with top of the range requirements.
Inspection Strategies for Dimensional Accuracy
Dimensional accuracy is significant for small portions, as even minor deviations can render them unusable. A number of strategies exist for verifying dimensional accuracy. Micrometers, calipers, and coordinate measuring machines (CMMs) are commonplace equipment used to measure linear dimensions. Those tools be offering excessive precision, enabling the detection of even minute diversifications. For advanced geometries, CMMs supply detailed three-D measurements, a very powerful for assessing intricate shapes and tolerances.
Optical comparators and laser interferometers will also be hired for correct measurements, particularly in eventualities hard excessive precision.
Inspection Strategies for Floor End
Keeping up a constant and desired floor end is similarly essential in milling small portions. Floor roughness impacts the phase’s aesthetic enchantment, its capability, and its resistance to corrosion. Profilometers and floor roughness measuring tools are used to quantify floor roughness, comparing parameters like Ra (reasonable roughness). Visible inspection, whilst much less exact, can temporarily establish important floor defects equivalent to scratches, pits, or unevenness.
Optical microscopy, regularly coupled with symbol research instrument, provides an in depth view of floor textures, helping in detecting delicate irregularities.
Examples of Inspection Gear and Ways
- Micrometers: Used for exact dimension of linear dimensions, crucial for checking the diameters, thicknesses, and lengths of small portions.
- Calipers: Flexible equipment for measuring distances between two issues. They’re handy for checking exterior and inner dimensions, helpful for fast exams of smaller portions.
- Coordinate Measuring Machines (CMMs): Subtle apparatus in a position to measuring advanced geometries in 3 dimensions. CMMs supply correct measurements of intricate shapes and tolerances.
- Profilometers: Tools for comparing floor roughness. They measure floor texture, offering knowledge on parameters like Ra (reasonable roughness), which is a very powerful for figuring out the outside high quality of the milled portions.
Flowchart of a Standard High quality Regulate Procedure
The flowchart illustrates an ordinary high quality keep watch over procedure for milled small portions. It starts with receiving uncooked fabrics, adopted by way of verifying their specs in opposition to requirements. Subsequent, the method comes to analyzing the milled portions at more than a few phases, making sure they agree to the design specs. This inspection procedure encompasses checking dimensions, floor end, and different essential parameters. Therefore, a last inspection confirms that the portions meet all high quality necessities ahead of unencumber. Documentation and reporting of inspection effects are a very powerful steps, as they supply information of the method and make allowance for research and development.
Protection Procedures and Precautions
Protected operation of milling machines is paramount, particularly when running with small steel portions. Neglecting protection protocols may end up in severe accidents, harm to apparatus, or even fatalities. This phase Artikels crucial protection procedures and precautions to make sure a protected and productive milling setting.Running milling machines calls for meticulous consideration to protection. Incorrect procedures may end up in injuries, and figuring out and imposing protection measures are a very powerful for fighting accidents.
Adherence to protection laws isn’t just a demand however a elementary duty for any individual working milling machines.
Very important Protection Precautions
Following established protection protocols is significant for fighting injuries throughout steel milling. Those protocols quilt more than a few facets, from private protecting apparatus to emergency procedures. Failure to stick to those tips may end up in critical penalties.
- System Guarding: Making sure correct device guarding is paramount. All uncovered shifting portions, such because the spindle and cutters, should be successfully shielded to forestall unintentional touch. This saves operators from harm and maintains the integrity of the device.
- Right kind Tooling: The usage of suitable and correctly maintained tooling is very important. Broken or worn-out equipment may cause sudden malfunctions and pose a vital possibility. Common inspections and replacements are essential for keeping up protection.
- Paintings House Group: Keeping up a blank and arranged paintings space is significant. Litter and particles may end up in slips, journeys, and falls, expanding the chance of injuries. Right kind group guarantees a more secure and extra environment friendly paintings setting.
Private Protecting Apparatus (PPE)
Suitable private protecting apparatus (PPE) is a cornerstone of protection in any milling operation. It safeguards the operator from doable hazards.
- Eye Coverage: Protection glasses or face shields are a very powerful to offer protection to the eyes from flying chips, steel fragments, and different particles. The danger of eye accidents is considerable in milling operations, and correct eye coverage can save you severe harm.
- Listening to Coverage: Milling machines can generate important noise ranges, which will reason listening to loss through the years. Listening to coverage, equivalent to earplugs or earmuffs, is very important for protecting listening to well being.
- Hand Coverage: Protecting gloves are crucial to offer protection to arms from cuts, abrasions, and doable touch with hazardous fabrics. Right kind hand coverage is a elementary protection measure.
- Foot Coverage: Protection sneakers or steel-toed boots are essential to offer protection to the toes from falling gadgets or different hazards provide within the milling setting. Protective toes from doable accidents is significant.
Emergency Procedures
Having well-defined emergency procedures in position is essential. A transparent course of action guarantees that staff know the way to react in case of an twist of fate or emergency.
- Emergency Prevent Procedures: The positioning and serve as of the emergency prevent button must be obviously marked and readily obtainable. Familiarity with the emergency prevent process is very important for preventing the device straight away in case of an twist of fate.
- First Assist and Clinical Help: A delegated first assist equipment and a plan for contacting scientific execs in case of an harm are essential. Rapid reaction and get right of entry to to scientific consideration are paramount.
- Fireplace Protection Procedures: Understanding find out how to react to a hearth, together with the site of fireside extinguishers and emergency exits, is essential. Fireplace protection protocols are essential to reduce the chance of fire-related incidents.
Protection Rules and Requirements
Adherence to protection laws and requirements is significant for a protected milling setting. Those requirements offer protection to employees and make sure the device’s integrity.
- OSHA Rules: OSHA (Occupational Protection and Well being Management) laws supply complete tips for place of work protection, together with particular necessities for milling device operations. Following OSHA requirements is very important for fighting place of work injuries.
- Business Requirements: Business-specific requirements would possibly additional give a boost to protection protocols. Those requirements would possibly be offering further safeguards or perfect practices, bettering the protection of the milling setting.
- Corporate Insurance policies: Firms working milling machines must identify their very own protection insurance policies and procedures, supplementing trade and executive laws. Those insurance policies make sure that all staff adhere to protection requirements.
Case Research and Examples
Actual-world programs of milling small steel portions are numerous and demanding throughout more than a few industries. From intricate watch parts to specific scientific implants, the facility to exactly form small steel items is very important. Working out the sensible programs, the benefits and drawbacks of various milling strategies, and the way design alternatives affect the milling procedure is essential to environment friendly and cost-effective production.
Actual-International Packages in Microelectronics
Microelectronics production is predicated closely on exact milling. For example, growing intricate circuit forums calls for milling tiny vias (through-holes) and strains (undertaking paths) with remarkable accuracy. This necessitates using high-precision milling machines, specialised reducing equipment, and strict adherence to dimensional tolerances. Milling strategies like ball-end milling are regularly most popular for his or her talent to supply clean surfaces in those essential programs.
Moreover, micro-milling equipment with extraordinarily small reducing diameters are crucial for attaining the specified degree of element. The precision calls for regularly necessitate specialised tooling fabrics and cooling fluids to mitigate warmth buildup and deal with floor end.
Milling of Clinical Implants
The manufacturing of scientific implants regularly comes to advanced milling processes. The high-precision milling of titanium alloys, for instance, is essential in growing biocompatible and sturdy implants like hip replacements and knee caps. Prime-precision milling guarantees a clean floor end and minimum burrs, a very powerful for the protection and longevity of the implant. The milling procedure should be moderately monitored to deal with the implant’s supposed form and dimensions.
Subject matter variety is significant on this utility, as biocompatibility and energy are paramount.
Benefits and Disadvantages of Other Milling Strategies in Particular Packages
Milling Means | Benefits | Disadvantages | Appropriate Software |
---|---|---|---|
Ball-end milling | Produces clean surfaces, appropriate for intricate shapes, excessive subject material elimination charges | Will also be much less exact for very tight tolerances, would possibly induce vibrations at excessive speeds | Microelectronics, scientific implants (with appropriate device measurement) |
Finish-milling | Flexible, environment friendly for greater portions, usually cost-effective | Is probably not as exact as ball-end milling for small, intricate options | Normal small phase machining, the place excessive precision isn’t essential |
Face milling | Prime subject material elimination charge, appropriate for enormous flat surfaces | Much less exact for small options, doubtlessly creates burrs if no longer correctly controlled | Bulk elimination, preparation of surfaces for additional machining |
The collection of milling manner immediately affects the manufacturing charge and high quality. Finish-milling, for instance, provides a steadiness between pace and price, making it appropriate for plenty of common machining duties. Then again, for very bits and bobs, ball-end milling is the awesome choice. Deciding on the right kind manner relies closely at the particular necessities of the phase.
Design Concerns for Milling Small Portions
Design options considerably affect the milling procedure and the general phase high quality. Attention must be given to device get right of entry to, chip evacuation, and the fabric’s houses. Designing with overhangs and undercuts in thoughts can considerably have an effect on milling feasibility. Good enough clearance for the reducing equipment is very important for fighting collisions and making sure clean operation.
Instance: Affect of Design Options on Milling Processes
Imagine a small steel phase with a deep hollow space. A poorly designed hollow space would possibly make it tough for the reducing device to get right of entry to the ground, doubtlessly inflicting the device to bind or fracture. A well-designed hollow space, with correct draft angles and enough clearance, guarantees environment friendly subject material elimination and minimizes the chance of device failure. In a similar way, a component with intricate inner options necessitates using specialised equipment and milling methods to succeed in the specified precision.
Ultimate Abstract
Effectively milling small steel portions calls for a deep figuring out of subject material variety, tooling, and design. By means of following the rules Artikeld right here, you’ll be able to be well-equipped to take on any small-scale metalworking problem with self assurance. The hot button is mastering the intricate steadiness between design, procedure, and high quality keep watch over. Include the precision and doable of steel milling!
Normal Inquiries
What are the commonest fabrics used for milling small steel portions?
Not unusual fabrics come with metallic alloys, aluminum, brass, and copper, each and every with various houses affecting machinability and energy. Selecting the proper subject material is determined by the particular utility and desired result.
How do I select the fitting milling device for small portions?
Smaller portions regularly require specialised milling machines with upper precision and smaller device functions. Imagine elements like the scale of the workpiece, desired accuracy, and the complexity of the milling operation when choosing the right device.
What protection precautions must I take when working a milling device?
At all times put on suitable private protecting apparatus (PPE), together with protection glasses, earplugs, and gloves. Apply all protection laws and perceive emergency procedures in case of injuries. Right kind device setup and upkeep also are essential for protection.
What are some commonplace design concerns for milling small portions?
Designing for environment friendly milling comes to minimizing subject material waste, optimizing reducing paths, and making sure correct give a boost to for the workpiece. Tooling barriers and phase geometry must be regarded as for the most efficient effects.